PV MODULE PERFORMANCE TEST
Analysis of the modules I-V characteristic, efficiency measurement and insulation, thermographic analysis.

DC INSULATION AND CONTINUITY TEST
Analysis and checks on the DC side of a plant. Verification of Continuity and Insulation Resistance.
COMPLETE TEST OF PHOTOVOLTAIC PLANT
Testing of an entire photovoltaic system. Measurement of global losses of the photovoltaic system.
FLUORESCENCE PV MODULE TEST
Pv module Fluorescence test on site, for cracks, EVA degradation and delamination detection.
PID POTENTIAL INDUCED DEGRADATION
PID (Potential Induced Degradation). Problem description and methods for photovoltaic modules testing.

PV MODULES ELECTRO LUMINESCENCE
Outdoor Electroluminescence on site for photovoltaic modules. Case studie and methodology.
PV PLANT DRONE THERMOGRAPHY
Execution of photovoltaic modules thermography with drone. Layout of thermal defects.
MODULES PID ONLINE CALCULATOR
Online PID Calculator. To perform an initial check for PID presence in your photovoltaic modules.
PHOTOVOLTAIC PLANT HI RESOLUTION THERMOGRAPHY WITH FLIR MSX TECHNOLOGY
The analysis with infrared camera is becoming increasingly important in the field of technical checks on photovoltaic systems. But what can be detected through this analysis of photovoltaic modules? When a cell does not work or generates energy because it is not receiving solar radiation, it may be inversely polarized. It will therefore behave as if it were charging rather than a generator, which could result in a high heat dissipation. This situation is easily identifiable with the use of a thermal imaging camera.
Photovoltaic panels can be inspected with a thermal imager from the front or back of the panel. The latter type of inspection has the advantage of avoiding problems related to solar reflections or reflections due to the low radiance associated with the crystalline surface of the panel or to a defective rear junction box. In any case, thermography allows you to quickly and remotely identify panels with hot spots. Then proceed quickly to solve problems related to production losses by repairing or replacing faulty photovoltaic modules.
Let's see what may be the main defects detectable with the thermography:
1) HOT SPOT (hot point due to defective, broken or malfunctioning cells)
Hot-Spot is a typically degenerative phenomenon that affects some photovoltaic modules. It occurs during the operation of the plant, even in conditions of moderate irradiation, due to partial shading of the modules or dirt located on individual photovoltaic cells. Its most obvious external manifestation is the considerable increase in the temperature of the cell affected by the problem with local temperatures that can safely exceed 100 ° C. See the following image:
As you can see, the yellow cell, or the warmest one, has a temperature difference of about 31 ° C compared to the other cells of the photovoltaic module. Deepening the analysis with the survey of the curve IV of the module (or measuring the loss of efficiency of the same photovoltaic module) you can find out how much the damaged cell reduces the total power produced and you can evaluate the possible replacement under warranty (if in progress validity) of the same form.
2) PID Effect (Potential Induced Degradation)
In the last period, there has been a confirmation from installers and managers of power loss plants and consequently of energy produced in photovoltaic systems. This phenomenon has been known in the literature since 1970 and was subsequently studied, analyzed and tested in June 2011 by the Fraunhofer Center for Silicon Photovoltaics which published the results of a test, according to which the PID is responsible for a reduction in power almost 70%.
Continua a leggere su Green Planner Magazine: Impianti fotovoltaici affetti da PID, come recuperare il ROI http://www.greenplanner.it/2015/01/14/impianti-fotovoltaici-affetti-da-pid-come-recuperare-il-roi/
Continua a leggere su Green Planner Magazine: Impianti fotovoltaici affetti da PID, come recuperare il ROI http://www.greenplanner.it/2015/01/14/impianti-fotovoltaici-affetti-da-pid-come-recuperare-il-roi/
Continua a leggere su Green Planner Magazine: Impianti fotovoltaici affetti da PID, come recuperare il ROI http://www.greenplanner.it/2015/01/14/impianti-fotovoltaici-affetti-da-pid-come-recuperare-il-roi/
This phenomenon occurs in particular in the PV module that is closest to the negative pole (Figures 1 and 2). The potential (ground voltage) of solar cells is usually between -200 V and -350 V, depending on the length of a string and the type of inverter used. The structure of the PV modules instead indicates a potential of 0 V, since it must be grounded for safety reasons.
Because of this voltage between solar cells and structure it can happen that the electrons break away from the materials used in the PV module and flow into the grounding structure (figure 1). This leaves a charge (polarization), which can negatively modify the characteristic curve of the solar cells (figure 2). It has been shown that these polarizations are mostly reversible. Therefore it is distinguished from irreversible effects, such as corrosion and normal aging.
Below you can see the thermography of a photovoltaic module affected by PID:
As you can see, the cells closest to the edge of the module are more superheated, indicating a loss of power of the same cells by PID effect. Performing the I-V analysis of the same module we can observe the decrease due to the defect detected with the thermography (module efficiency dropped to -49.83%):
In conclusion, it can be said that the infrared (IR) inspection of photovoltaic systems allows to quickly identify potential defects at the cell and module level and possible problems of electrical interconnection. The inspections are carried out under normal operating conditions and do not require the shutdown of the system. Inspections with a thermal imager - from quality control during installation, followed by regular checks - facilitate simple but complete monitoring of the system conditions. This will help conserve the functionality of the solar panels and prolong their life. The use of thermal imaging cameras for solar panel inspections will therefore drastically improve the company's return on investment.
Download an example thermographic report performed on some photovoltaic modules.
CONTACT US FOR TECHNICAL ANALYSIS OF YOUR PHOTOVOLTAIC PLANT
We are available for individuals and installers for technical inspection and expertise also for legal disputes use.
Contact us info@st-ingegneria.com
BROCHURE - REFERENCES
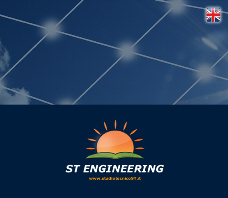
OUR SERVICES
- Instrumental checks on photovoltaic
- Technical Due Diligence for PV plant
- Energy plant engineering design
- SPI, SPG verification AEEG 786/2016
- Photovoltaic Thermography
- Photovoltaic plant full test CEI 82-25
- Grid parameters quality analysis
- Drone Thermography
- Outdoor Ectroluminescence on site
- Relay test verification
- Law 96/2017 non certified modules
- Transformer removal for CEI 0-21